Réussir son Plan de Maintenance Industrielle : Astuces et Solutions
La maintenance industrielle joue un rôle fondamental dans le secteur industriel, étant une pierre angulaire qui garantit non seulement le bon fonctionnement des équipements mais aussi leur longévité. Cette importance s’étend bien au-delà de la simple réparation des machines : elle est cruciale pour assurer la sécurité des employés, minimiser les temps d’arrêt imprévus et optimiser la productivité. Dans un contexte où les industries sont de plus en plus compétitives et où la technologie évolue rapidement, un plan de maintenance industriel efficace n’est plus une option mais une nécessité. Ce plan doit être méticuleusement élaboré, en tenant compte des spécificités de chaque équipement et des différents types de maintenance requis. L’objectif est de prévenir les pannes avant qu’elles ne surviennent, tout en optimisant les ressources et en réduisant les coûts. Ainsi, la maintenance industrielle devient un facteur clé non seulement pour la continuité des opérations commerciales mais également pour la durabilité et l’efficience économique des entreprises.
L’objectif de cet article est de fournir un guide exhaustif et pratique pour la création d’un plan de maintenance industrielle efficace. Face à l’évolution rapide des technologies et des méthodes de maintenance, il est impératif pour les responsables et les techniciens de maintenance de rester informés et compétents. Cet article vise donc à démystifier le processus de création d’un tel plan, en couvrant toutes ses étapes clés, depuis l’analyse initiale des besoins jusqu’à l’implémentation et le suivi des stratégies de maintenance. Nous aborderons les différents types de maintenance – préventive, prédictive et corrective – tout en mettant l’accent sur l’importance de la formation du personnel et l’utilisation des nouvelles technologies. Que vous soyez un professionnel chevronné de la maintenance industrielle ou un novice dans le domaine, cet article est conçu pour vous fournir les connaissances et les outils nécessaires pour élaborer un plan de maintenance robuste et adapté à vos besoins spécifiques.
Qu’est-ce que la maintenance industrielle ?
La maintenance industrielle est définie comme l’ensemble des actions techniques, administratives et de gestion qui permettent de maintenir ou de rétablir un équipement, une machine ou un système dans un état spécifié afin qu’ils puissent assurer un service déterminé. Cette discipline englobe une large gamme d’activités, allant de l’inspection régulière et l’entretien préventif jusqu’aux réparations et remplacements nécessaires en cas de panne. Le but principal de la maintenance industrielle est de prévenir les défaillances des équipements, d’assurer leur fonctionnement optimal et de prolonger leur durée de vie utile. Elle joue un rôle crucial dans la minimisation des arrêts de production, la garantie de la sécurité et la réduction des coûts opérationnels. Dans un environnement industriel en constante évolution, où la technologie et les exigences de production se transforment rapidement, la maintenance industrielle doit également s’adapter, intégrant de nouvelles méthodes et technologies pour rester efficace et pertinente.
Il existe plusieurs types de maintenance industrielle, chacun répondant à des besoins et des stratégies spécifiques. La maintenance préventive est l’une des plus courantes, consistant à réaliser des interventions régulières et planifiées pour prévenir les pannes. Ces activités sont généralement basées sur des intervalles de temps prédéterminés ou des indicateurs de performance des équipements. Ensuite, la maintenance prédictive, qui s’appuie sur l’utilisation de technologies avancées pour surveiller en continu l’état des équipements et prédire les défaillances avant qu’elles ne surviennent. Cette approche permet une planification plus précise des interventions de maintenance et aide à éviter les arrêts inattendus. La maintenance corrective, quant à elle, intervient après la détection d’une panne ou d’un dysfonctionnement, et a pour but de rétablir l’équipement dans son état de fonctionnement normal. Chaque type de maintenance a son importance et, dans un plan de maintenance industriel efficace, une combinaison de ces différentes méthodes est souvent utilisée pour assurer une gestion optimale des équipements.
Les enjeux de la maintenance industrielle
La sécurité est l’un des enjeux majeurs de la maintenance industrielle. Un équipement mal entretenu peut présenter des risques significatifs pour la sécurité des opérateurs et de l’environnement de travail. Les accidents liés aux équipements peuvent être graves, voire mortels, et entraîner des conséquences juridiques et financières importantes pour l’entreprise. Une maintenance régulière et bien planifiée permet de détecter et de corriger les défauts susceptibles de provoquer des accidents, assurant ainsi un environnement de travail plus sûr. De plus, elle permet de s’assurer que les équipements sont conformes aux normes et réglementations en vigueur. La sécurité ne concerne pas seulement les opérateurs, mais aussi la pérennité de l’ensemble de l’infrastructure industrielle.
La productivité est étroitement liée à l’efficacité de la maintenance industrielle. Des équipements bien entretenus fonctionnent de manière optimale, ce qui réduit les temps d’arrêt imprévus et augmente la capacité de production. Un plan de maintenance efficace permet de planifier les interventions de manière à minimiser l’impact sur la production. Par exemple, les tâches de maintenance préventive peuvent être programmées pendant les périodes de faible activité, ce qui réduit les perturbations. En outre, la maintenance prédictive, grâce à l’analyse des données et à la surveillance continue, permet d’anticiper les pannes potentielles et de prendre des mesures préventives sans interrompre la production. Cela assure une utilisation maximale des équipements et une réduction des coûts de production dus aux arrêts imprévus.
La durabilité est un autre aspect crucial de la maintenance industrielle. Un entretien régulier prolonge la durée de vie des équipements, ce qui est non seulement économiquement avantageux mais aussi écologiquement bénéfique. En évitant les remplacements fréquents d’équipements, les entreprises réduisent leur empreinte écologique et contribuent à une utilisation plus durable des ressources. De plus, la maintenance permet d’optimiser l’efficacité énergétique des machines, réduisant ainsi la consommation d’énergie et les émissions de gaz à effet de serre. Dans un contexte où les préoccupations environnementales deviennent de plus en plus prégnantes, adopter des pratiques de maintenance qui soutiennent la durabilité est essentiel pour les entreprises qui cherchent à réduire leur impact sur l’environnement tout en améliorant leur image de marque et leur conformité réglementaire.
Principes de base pour un plan de maintenance
La planification est le premier pilier d’un plan de maintenance industrielle efficace. Elle implique la mise en place d’un calendrier détaillé des activités de maintenance, basé sur une évaluation approfondie des besoins de chaque équipement. Cette étape nécessite une compréhension claire des cycles de vie des machines, de leur historique de pannes et de leur importance dans le processus de production. Une planification efficace permet de réduire les interruptions imprévues et d’optimiser l’utilisation des ressources. Elle inclut également la préparation des procédures d’intervention, la définition des rôles et responsabilités de chaque membre de l’équipe de maintenance, ainsi que la coordination avec les autres départements pour minimiser l’impact sur la production.
L’organisation concerne la mise en place des structures et des processus nécessaires pour exécuter le plan de maintenance. Cela inclut la gestion des équipes de maintenance, la répartition des tâches, la coordination des interventions et la gestion des outils et des pièces de rechange. Une bonne organisation permet d’assurer que les interventions de maintenance sont réalisées de manière efficace et en temps voulu. Il est également important d’établir des procédures claires pour répondre aux urgences et aux pannes imprévues. L’organisation efficace de la maintenance aide à maintenir une haute qualité de service et à maximiser la disponibilité des équipements.
La gestion des ressources est essentielle pour assurer que l’équipe de maintenance dispose de tout ce dont elle a besoin pour effectuer son travail. Cela comprend la gestion des stocks de pièces de rechange, des outils et équipements de maintenance, ainsi que la gestion du personnel. La gestion efficace des ressources implique également un suivi rigoureux des coûts et des dépenses liés à la maintenance, afin d’optimiser le budget et d’éviter les gaspillages. De plus, il est important d’évaluer régulièrement les compétences et les besoins en formation du personnel de maintenance pour s’assurer qu’ils restent à jour avec les technologies et pratiques les plus récentes. Une gestion des ressources efficace contribue à améliorer l’efficacité globale du plan de maintenance et à réduire les coûts à long terme.
Analyse des besoins en maintenance
L’évaluation des équipements est une étape cruciale dans l’analyse des besoins en maintenance. Elle implique un examen approfondi de chaque machine ou système pour déterminer son état actuel et son niveau de performance. Cette évaluation peut inclure des inspections visuelles, des tests de fonctionnement, et l’utilisation de technologies de diagnostic avancées, comme l’analyse des vibrations ou la thermographie. L’objectif est de détecter tout signe de dégradation ou de dysfonctionnement qui pourrait nécessiter une intervention de maintenance. Cette étape permet également d’identifier les équipements qui sont critiques pour la production et qui nécessitent une attention particulière. Une évaluation précise et régulière des équipements est essentielle pour planifier efficacement les activités de maintenance et pour éviter les pannes inattendues.
L’examen de l’historique des pannes joue un rôle important dans l’élaboration d’un plan de maintenance. Cette analyse permet d’identifier les tendances et les motifs récurrents de défaillance, offrant ainsi des indications précieuses sur les vulnérabilités potentielles des équipements. L’étude de l’historique des pannes aide à comprendre les causes racines des problèmes et à développer des stratégies pour les prévenir à l’avenir. Il est important de tenir des registres détaillés de toutes les pannes, interventions de maintenance et réparations effectuées, car ces données fournissent une base solide pour l’amélioration continue des pratiques de maintenance. L’analyse de l’historique des pannes est également un outil précieux pour la formation du personnel de maintenance, leur permettant de mieux anticiper et gérer les problèmes similaires à l’avenir.
Les prévisions de maintenance sont une composante clé de la planification stratégique. Elles impliquent l’utilisation de données historiques et d’analyses prédictives pour anticiper les besoins futurs en maintenance. Cela peut inclure la planification des remplacements de pièces usées, l’identification des périodes de maintenance optimales et la préparation des ressources nécessaires. Les prévisions aident à transformer la maintenance d’une activité réactive à une démarche proactive, permettant ainsi de mieux gérer les ressources et de réduire les interruptions de production. L’utilisation de logiciels de gestion de maintenance assistée par ordinateur (GMAO) peut grandement faciliter ce processus en automatisant la collecte et l’analyse des données. En anticipant les besoins futurs, les entreprises peuvent planifier leurs activités de maintenance de manière plus efficace, garantissant ainsi une performance optimale des équipements et une production ininterrompue.
Élaboration du plan de maintenance
L’élaboration d’un plan de maintenance industrielle efficace implique plusieurs étapes clés. La première étape est l’évaluation des besoins de maintenance pour chaque équipement, qui se base sur les inspections, l’historique des pannes et les prévisions. Ensuite, il faut définir les objectifs de maintenance spécifiques à l’entreprise, tels que l’amélioration de la fiabilité des équipements ou la réduction des coûts de maintenance. Après avoir fixé ces objectifs, la prochaine étape consiste à élaborer des stratégies de maintenance adaptées, en choisissant entre maintenance préventive, prédictive ou corrective, selon les besoins. Cela inclut la planification des tâches de maintenance, la détermination des fréquences d’intervention et l’allocation des ressources nécessaires. Enfin, le plan doit être documenté et communiqué clairement à toutes les parties prenantes, avec des procédures détaillées et un calendrier des interventions.
Les outils nécessaires pour mettre en œuvre un plan de maintenance industrielle varient en fonction de la complexité des équipements et des objectifs de maintenance. Les outils de base comprennent des logiciels de gestion de la maintenance (comme des systèmes de GMAO), qui permettent de suivre les tâches de maintenance, de gérer les stocks de pièces de rechange et de documenter l’historique des interventions. Des outils de diagnostic avancés, tels que des analyseurs de vibrations, des caméras thermiques ou des capteurs de condition, sont également importants pour la maintenance prédictive. En outre, il est essentiel de disposer d’un inventaire bien géré de pièces de rechange et d’outils de maintenance. La formation et le développement des compétences du personnel de maintenance sont aussi des outils clés, car ils garantissent que les opérations de maintenance sont effectuées de manière compétente et sécuritaire. La sélection et l’utilisation appropriées des outils sont cruciales pour l’efficacité et la réussite du plan de maintenance.
Stratégies de maintenance efficaces
La maintenance préventive est une stratégie proactive qui consiste à effectuer des interventions régulières et planifiées pour prévenir les défaillances des équipements. Ce type de maintenance se base sur un calendrier établi selon le temps ou le cycle d’utilisation des équipements. Les activités typiques de maintenance préventive incluent le nettoyage, la lubrification, les ajustements, les remplacements de pièces usées et les inspections régulières. L’avantage principal de cette approche est la réduction significative des pannes inattendues, ce qui entraîne une meilleure fiabilité et disponibilité des équipements. Pour mettre en œuvre efficacement la maintenance préventive, il est essentiel de disposer de données précises sur les équipements et de suivre un programme de maintenance rigoureux. Cela implique également une formation adéquate du personnel pour qu’ils puissent réaliser les tâches de maintenance en respectant les normes et procédures établies.
La maintenance prédictive va un pas plus loin que la maintenance préventive en utilisant des données et des analyses pour prédire les défaillances avant qu’elles ne surviennent. Cette approche s’appuie sur des technologies telles que la surveillance des conditions, l’analyse des vibrations, la thermographie et l’analyse d’huile. En surveillant en continu les signes vitaux des équipements, les techniciens peuvent détecter les anomalies et intervenir avant que les problèmes ne deviennent critiques. La maintenance prédictive permet une gestion des ressources plus efficace, car les interventions sont réalisées uniquement lorsque les indicateurs suggèrent une dégradation imminente. Cela contribue à une réduction des coûts de maintenance et à une amélioration de la durée de vie des équipements. La mise en œuvre de la maintenance prédictive nécessite un investissement initial dans la technologie de surveillance et une compétence analytique, mais les économies à long terme et l’amélioration de la fiabilité en valent la peine.
La maintenance corrective est effectuée après qu’une panne ou un dysfonctionnement s’est produit. Son objectif est de réparer ou de remplacer les équipements défectueux pour rétablir leur fonctionnement normal. Bien que cette approche soit souvent perçue comme moins idéale que la maintenance préventive ou prédictive, elle reste une composante essentielle d’un plan de maintenance global. Dans certains cas, la maintenance corrective peut être la méthode la plus économique, surtout pour les équipements moins critiques ou ceux dont les défaillances ne présentent pas de risques majeurs pour la production. La clé d’une maintenance corrective efficace réside dans une intervention rapide et compétente pour minimiser les temps d’arrêt et les impacts sur la production. Il est donc crucial d’avoir un personnel bien formé et prêt à répondre rapidement, ainsi qu’un stock adéquat de pièces de rechange pour effectuer les réparations de manière efficace.
Formation et compétences du personnel
La formation du personnel joue un rôle essentiel dans la réussite d’un plan de maintenance industrielle. Un personnel bien formé est non seulement capable d’effectuer les tâches de maintenance de manière plus efficace, mais peut aussi mieux identifier les signes précurseurs de défaillances potentielles. La formation doit couvrir non seulement les compétences techniques nécessaires pour les différentes tâches de maintenance, mais aussi la compréhension des systèmes d’équipement, les procédures de sécurité, et l’utilisation des outils de diagnostic. Avec l’évolution rapide des technologies, la formation continue est indispensable pour maintenir les compétences du personnel à jour. Cela peut inclure des formations internes, des ateliers, des séminaires, ou même des certifications professionnelles. Investir dans la formation du personnel de maintenance augmente non seulement l’efficacité de la maintenance, mais renforce également la culture de la sécurité et améliore le moral des employés.
Les compétences requises pour le personnel de maintenance industrielle sont diverses et dépendent de la complexité des équipements et des spécificités de l’industrie. Les compétences techniques sont primordiales, incluant la connaissance des machines, la capacité à lire et à comprendre les plans et les schémas techniques, et les compétences en matière de réparation et d’entretien. Avec l’avènement de l’industrie 4.0, des compétences en informatique et en analyse de données deviennent de plus en plus importantes, en particulier pour ceux impliqués dans la maintenance prédictive. Outre les compétences techniques, les compétences interpersonnelles telles que la communication, la résolution de problèmes et le travail d’équipe sont essentielles pour une maintenance efficace. La capacité à travailler sous pression et à répondre rapidement aux situations d’urgence est également importante. Un personnel possédant un mélange équilibré de ces compétences est mieux équipé pour maintenir les équipements en bon état de fonctionnement et garantir la continuité des opérations industrielles.
Utilisation des technologies modernes
L’utilisation de logiciels de gestion de maintenance assistée par ordinateur (GMAO) est devenue un élément crucial dans la mise en œuvre d’un plan de maintenance efficace. Ces systèmes permettent de centraliser les informations concernant les équipements, les interventions de maintenance, les historiques de pannes et les stocks de pièces de rechange. Un logiciel de GMAO efficace offre plusieurs fonctionnalités, telles que la planification et le suivi des tâches de maintenance, la gestion des ordres de travail, et l’analyse des données de maintenance pour identifier les tendances et les domaines d’amélioration. Il facilite également la communication et la coordination au sein des équipes de maintenance et avec d’autres départements. L’adoption de ces logiciels permet non seulement d’augmenter l’efficacité opérationnelle, mais aussi de réduire les coûts en optimisant les ressources et en prévenant les pannes coûteuses.
L’automatisation et l’Internet des Objets (IoT) transforment la manière dont la maintenance industrielle est effectuée. Les capteurs IoT peuvent être installés sur les équipements pour surveiller en temps réel divers paramètres tels que la température, la pression, les vibrations, et plus encore. Ces données sont ensuite analysées pour détecter les anomalies qui pourraient indiquer un problème imminent. L’automatisation, quant à elle, permet de réaliser certaines tâches de maintenance de manière plus efficace et sécurisée, en particulier dans les environnements dangereux ou difficiles d’accès. L’intégration de l’IoT et de l’automatisation dans le plan de maintenance offre une approche plus proactive et prédictive, permettant de réduire significativement les temps d’arrêt et d’améliorer la longévité des équipements. De plus, ces technologies permettent une collecte de données plus précise et en grande quantité, ouvrant la voie à des analyses plus approfondies et à une meilleure prise de décision.
Gestion des pièces de rechange et des fournitures
La gestion de l’inventaire est un aspect fondamental de la maintenance industrielle. Elle implique la gestion et le suivi des stocks de pièces de rechange, des outils et des consommables nécessaires pour la maintenance. Une gestion efficace de l’inventaire assure que les pièces et les outils nécessaires sont disponibles au moment voulu, évitant ainsi des retards dans les interventions de maintenance. Il est important de maintenir un équilibre entre avoir suffisamment de stock pour répondre aux besoins de maintenance et éviter le surstockage, qui peut immobiliser des capitaux importants. Les logiciels de gestion d’inventaire peuvent être utilisés pour suivre les niveaux de stock, prévoir les besoins futurs en pièces de rechange, et passer des commandes automatiquement. Une bonne gestion de l’inventaire contribue à la réduction des coûts et à l’amélioration de l’efficacité des opérations de maintenance.
La relation avec les fournisseurs est un autre élément crucial dans la gestion de la maintenance. Choisir des fournisseurs fiables et établir de bonnes relations avec eux assure un approvisionnement régulier et de qualité des pièces de rechange et des matériaux nécessaires. Il est important de procéder à une évaluation minutieuse des fournisseurs en tenant compte de leur capacité à fournir des produits de qualité, leur fiabilité en termes de délais de livraison, et leur flexibilité pour répondre aux demandes urgentes. La négociation de contrats à long terme avec des fournisseurs de confiance peut également contribuer à réduire les coûts. Dans certains cas, il peut être avantageux de développer des partenariats avec les fournisseurs pour garantir une meilleure intégration et coordination. Une gestion efficace des relations avec les fournisseurs est donc essentielle pour assurer un approvisionnement fluide et fiable, ce qui est un facteur clé pour le succès du plan de maintenance.
Évaluation et amélioration continue
Le suivi des performances est une composante essentielle de l’évaluation et de l’amélioration continue d’un plan de maintenance industrielle. Cette pratique implique la collecte et l’analyse régulières de données relatives aux activités de maintenance, telles que les temps de réponse aux pannes, la durée des réparations, la fréquence des défaillances, et le coût des interventions. L’objectif est de mesurer l’efficacité du plan de maintenance en place et d’identifier les domaines nécessitant des améliorations. Les indicateurs de performance clés (KPI) doivent être définis pour évaluer différents aspects de la maintenance, tels que la fiabilité des équipements, l’efficacité de la maintenance et la satisfaction des utilisateurs. Le suivi régulier de ces indicateurs aide à détecter les tendances, à anticiper les problèmes potentiels et à prendre des décisions éclairées pour optimiser le plan de maintenance. L’utilisation de logiciels de GMAO peut faciliter grandement ce suivi en automatisant la collecte et l’analyse des données.
La maintenance industrielle est un domaine dynamique, et il est important que le plan de maintenance évolue pour s’adapter aux changements dans l’environnement de production, aux nouvelles technologies et aux meilleures pratiques. Les mises à jour régulières du plan de maintenance sont nécessaires pour intégrer les leçons apprises, les résultats des évaluations de performance et les retours d’expérience des opérateurs et techniciens. Ces mises à jour peuvent inclure l’ajustement des procédures de maintenance, la révision des fréquences d’intervention, l’intégration de nouvelles technologies de maintenance, ou la formation supplémentaire du personnel. Un plan de maintenance doit être considéré comme un document vivant, sujet à des révisions et des améliorations continues pour s’assurer qu’il reste pertinent et efficace. L’implication et le feedback de l’ensemble des parties prenantes, y compris le personnel de maintenance, les opérateurs d’équipements et la direction, sont cruciaux pour garantir que le plan de maintenance réponde au mieux aux besoins de l’organisation.
Cas pratiques et exemples réussis
Les études de cas sont un outil précieux pour comprendre comment des plans de maintenance industrielle efficaces sont mis en œuvre dans la pratique. Elles fournissent des exemples concrets de la manière dont différentes entreprises ont abordé la maintenance de leurs équipements, les défis rencontrés et les solutions adoptées. L’analyse d’études de cas aide à identifier les meilleures pratiques et les stratégies qui ont fait leurs preuves dans des contextes similaires. Elle permet également de tirer des leçons des erreurs et des réussites d’autres organisations. Ces études peuvent couvrir une variété de secteurs industriels et de technologies, offrant ainsi une perspective large et diversifiée. Intégrer les enseignements tirés des études de cas dans le plan de maintenance peut contribuer à améliorer son efficacité et à éviter les écueils courants.
Les témoignages de techniciens, d’ingénieurs de maintenance et de gestionnaires d’usine fournissent un aperçu précieux des aspects pratiques et opérationnels de la maintenance industrielle. Ils offrent des perspectives de terrain sur les défis quotidiens, les stratégies réussies et les astuces pour gérer efficacement les opérations de maintenance. Les témoignages peuvent également révéler comment les changements dans le plan de maintenance affectent le personnel et la production. Ils sont particulièrement utiles pour comprendre l’impact humain et organisationnel des décisions de maintenance, offrant une dimension supplémentaire qui va au-delà des données et des statistiques. Écouter et intégrer les retours d’expérience des personnes directement impliquées dans les activités de maintenance peut enrichir considérablement le plan de maintenance, le rendant plus adapté et réaliste.
Défis et solutions courantes
Dans le domaine de la maintenance industrielle, plusieurs problèmes fréquents peuvent survenir, affectant la performance et l’efficacité des équipements. Parmi ces problèmes, on trouve souvent des pannes récurrentes dues à un manque de maintenance préventive, des erreurs humaines résultant d’une formation insuffisante ou d’une mauvaise compréhension des procédures, et des problèmes liés à l’usure naturelle des équipements. D’autres défis courants incluent la gestion inefficace des pièces de rechange, conduisant à des retards dans les réparations, et les difficultés à intégrer de nouvelles technologies dans les processus de maintenance existants. Identifier et comprendre ces problèmes fréquents est crucial pour développer des stratégies efficaces pour les prévenir et les gérer. Une analyse approfondie des causes racines de ces problèmes permet d’apporter des améliorations ciblées au plan de maintenance.
Pour chaque problème commun identifié dans la maintenance industrielle, des solutions spécifiques peuvent être mises en œuvre. Face aux pannes récurrentes, l’adoption d’une maintenance préventive et prédictive peut aider à anticiper et à éviter les défaillances. En ce qui concerne les erreurs humaines, la formation continue et le renforcement des procédures de sécurité sont essentiels. Pour résoudre les problèmes d’usure naturelle, il est important d’établir un calendrier de remplacement basé sur la durée de vie estimée des composants. En outre, une gestion efficace des stocks de pièces de rechange permet de réduire les délais de réparation. L’intégration de nouvelles technologies, telles que les systèmes de GMAO et l’IoT, peut moderniser et améliorer les processus de maintenance. Ces solutions nécessitent une approche holistique et une planification minutieuse pour être efficacement intégrées dans les pratiques de maintenance existantes.
À retenir
Importance Cruciale de la Maintenance Industrielle : La maintenance industrielle est essentielle pour assurer la sécurité, la productivité et la durabilité des équipements. Elle joue un rôle central dans la réduction des temps d’arrêt et l’optimisation des performances des machines.
Stratégies de Maintenance Adaptées : L’adoption de stratégies de maintenance, qu’elles soient préventives, prédictives ou correctives, doit être alignée avec les besoins spécifiques de chaque équipement et les objectifs globaux de l’entreprise.
Formation et Compétences du Personnel : La formation continue du personnel de maintenance est vitale. Elle garantit non seulement la réalisation efficace des tâches de maintenance, mais aussi la sécurité et la conformité aux normes en vigueur.
Utilisation des Technologies Modernes : L’intégration de technologies avancées, telles que les logiciels de GMAO et les capteurs IoT, améliore la précision et l’efficacité des opérations de maintenance.
Gestion Efficace des Ressources : Une gestion optimale des ressources, incluant l’inventaire des pièces de rechange et la relation avec les fournisseurs, est essentielle pour éviter les interruptions et réduire les coûts.
Suivi et Amélioration Continus : Le suivi régulier des performances et la mise à jour continue du plan de maintenance sont nécessaires pour s’adapter aux changements et améliorer constamment les processus.
Adaptation et Flexibilité : Un plan de maintenance doit être flexible et capable de s’adapter aux évolutions technologiques, aux changements dans les processus de production et aux retours d’expérience du personnel.
En résumé, la création et la mise en œuvre d’un plan de maintenance industrielle efficace nécessitent une approche holistique, intégrant des stratégies adaptées, la formation du personnel, l’utilisation des technologies modernes, une gestion efficace des ressources, ainsi qu’un suivi et une amélioration continus. C’est la clé pour garantir la fiabilité, la sécurité et l’efficacité opérationnelle dans le secteur industriel.
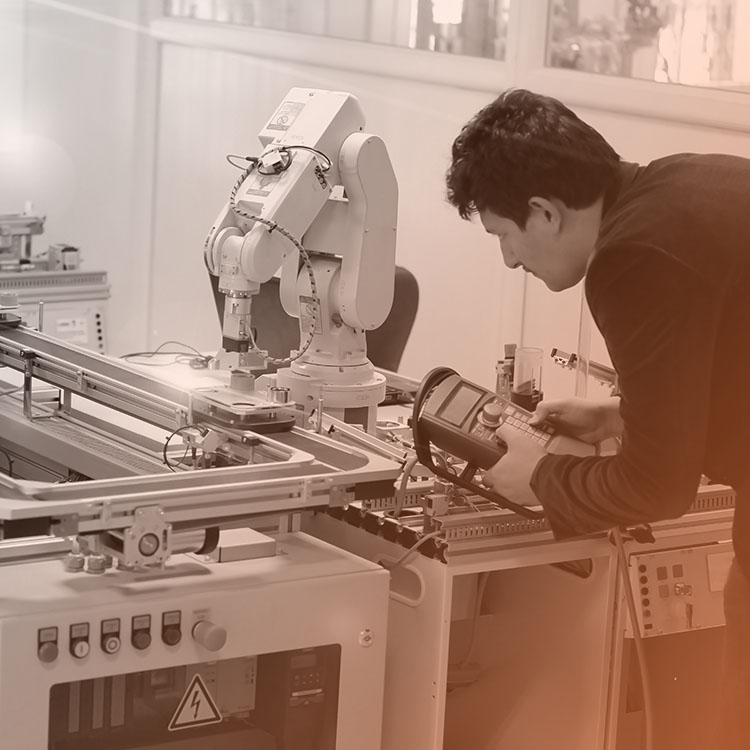
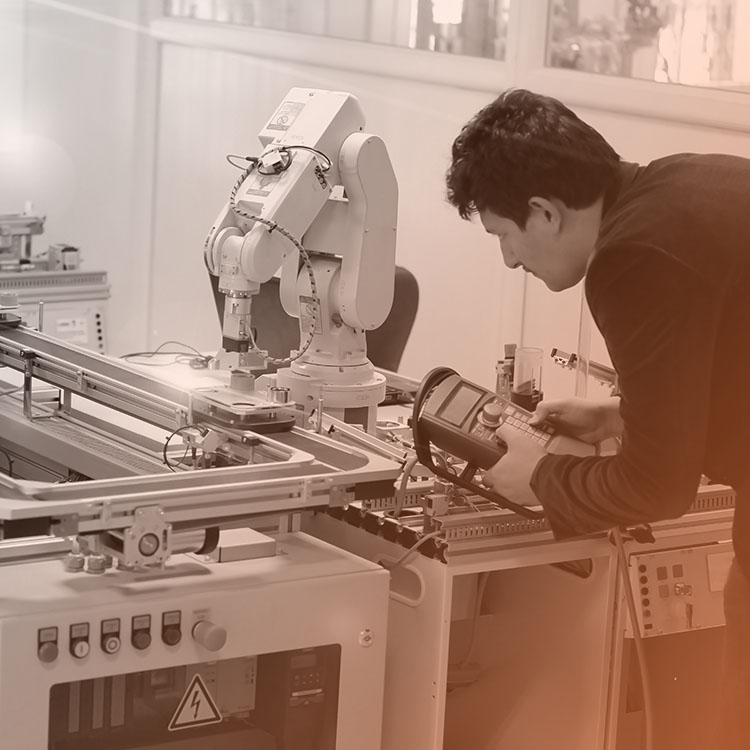
Nos offres
Simplifiez la gestion
de votre infrastructure
Notre plus grande fierté
Plus de 120 clients satisfaits:
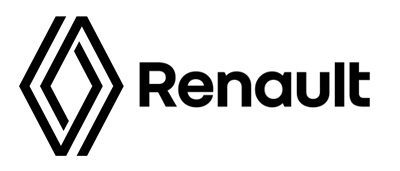
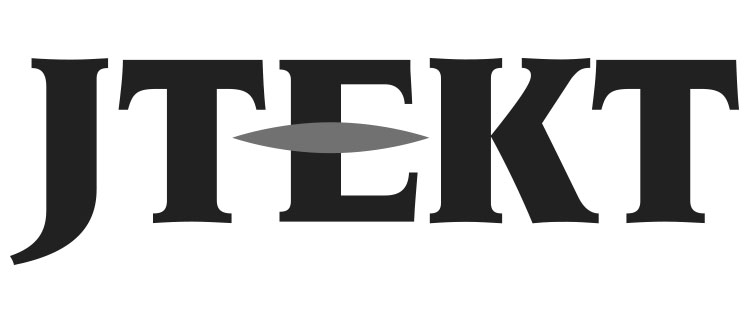
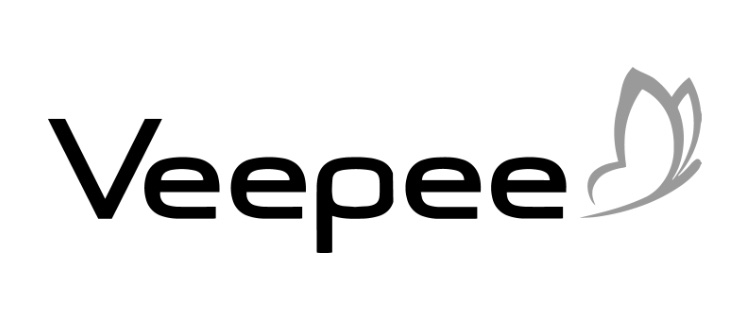
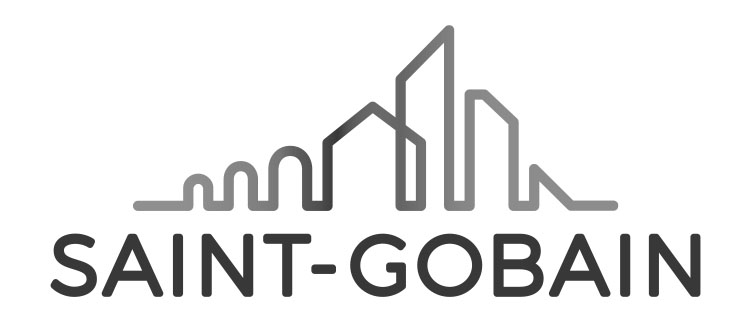
5
agences en France
8.3 M€
prévisionnel CA 2024
120
clients réguliers
24h
délai d’intervention
100