Les différents types de maintenance industrielle : la maintenance curative, la maintenance corrective, la maintenance prédictive, la maintenance préventive systématique et la maintenance préventive conditionnelle.
La maintenance curative, souvent considérée comme une approche réactive, est une composante essentielle de la gestion industrielle. Elle intervient après la survenue d’une défaillance ou d’un dysfonctionnement dans les équipements ou les systèmes. Cette forme de maintenance est cruciale car elle permet de rétablir rapidement le fonctionnement normal des machines et de minimiser les temps d’arrêt imprévus qui peuvent avoir des répercussions importantes sur la production. Dans la pratique, la maintenance curative peut impliquer des activités telles que la réparation d’urgence, le remplacement de pièces défectueuses ou la réalisation de réglages nécessaires pour remettre l’équipement en état de marche. Par exemple, si une chaîne de production s’arrête soudainement à cause d’une panne mécanique, l’intervention curative consisterait à identifier et à réparer le problème le plus rapidement possible. Bien que cette approche soit essentielle pour traiter les problèmes immédiats, elle est souvent perçue comme une solution à court terme. En effet, la maintenance curative ne prévient pas les pannes mais y répond après leur survenue. Elle est donc complémentaire aux autres formes de maintenance, comme la maintenance préventive ou prédictive, qui visent à anticiper et éviter les défaillances avant qu’elles ne se produisent. La maintenance curative joue un rôle indispensable dans la garantie de la continuité des opérations industrielles, en assurant que les pannes soient résolues efficacement et dans les plus brefs délais.
La maintenance curative
La maintenance curative, un élément central de la stratégie de maintenance industrielle, se définit par des interventions réactives visant à réparer des équipements après la survenue d’une panne ou d’un dysfonctionnement. Ce type de maintenance est crucial pour les industries car il assure la reprise rapide des opérations interrompues, minimisant ainsi les impacts négatifs sur la production. Concrètement, lorsqu’un équipement tombe en panne, des techniciens spécialisés procèdent à un diagnostic pour identifier la cause du problème, puis effectuent les réparations nécessaires, qui peuvent inclure le remplacement de pièces, les réglages mécaniques ou électriques, et d’autres ajustements techniques. Par exemple, dans une usine de fabrication, si une machine de production cesse de fonctionner en raison d’un composant défectueux, la maintenance curative consistera à remplacer ce composant pour que la machine puisse reprendre son fonctionnement normal. Cette approche est souvent considérée comme du « feu de brousse », car elle s’attaque aux problèmes au fur et à mesure qu’ils surviennent, sans planification préventive. Bien que cette méthode soit indispensable pour gérer les crises et les urgences, elle peut s’avérer coûteuse et moins efficace à long terme par rapport aux approches préventives ou prédictives.
La maintenance curative se manifeste dans divers contextes industriels à travers des exemples concrets. Dans l’industrie automobile, par exemple, si une chaîne de montage s’arrête soudainement à cause d’une défaillance du système pneumatique, la maintenance curative implique l’intervention rapide d’une équipe de maintenance pour diagnostiquer et résoudre le problème, souvent sous une pression de temps considérable pour limiter l’arrêt de production. Un autre exemple peut être trouvé dans le secteur des énergies renouvelables : si une éolienne cesse de fonctionner en raison d’une défaillance de son système de contrôle, la maintenance curative est nécessaire pour remplacer ou réparer les composants défectueux. L’utilité de la maintenance curative réside dans sa capacité à assurer la continuité des opérations en réduisant les temps d’arrêt imprévus. Elle est essentielle dans les environnements où les équipements sont cruciaux pour les opérations quotidiennes, comme dans les usines de production, les hôpitaux (pour les équipements médicaux) ou les centres de données. Toutefois, il est important de noter que la dépendance excessive à la maintenance curative peut conduire à des coûts de maintenance plus élevés et à une durée de vie réduite des équipements, soulignant ainsi la nécessité d’un équilibre avec des stratégies de maintenance plus proactives.
La maintenance corrective
La maintenance corrective est une stratégie clé dans la gestion des équipements industriels, centrée sur la correction des défauts et anomalies détectés dans les machines et systèmes. Contrairement à la maintenance curative, qui répond aux pannes après leur survenue, la maintenance corrective est souvent initiée suite à la détection d’un problème avant qu’une panne complète ne se produise. Cette forme de maintenance peut être le résultat d’inspections régulières, de contrôles de routine ou de systèmes de surveillance qui signalent des irrégularités. Par exemple, lors d’une inspection, si une usure anormale est détectée sur un composant d’une machine, la maintenance corrective consistera à remplacer ou réparer ce composant avant qu’il ne cause une panne majeure. Cette approche proactive aide à maintenir le bon fonctionnement des équipements, tout en prévenant les arrêts inopinés et coûteux. La maintenance corrective implique souvent une analyse approfondie des causes profondes des problèmes détectés, permettant ainsi de mettre en place des solutions durables. Elle est particulièrement utile dans les industries où la fiabilité et la performance continue des équipements sont essentielles, comme dans les secteurs de la fabrication, de l’énergie ou des transports. En somme, la maintenance corrective joue un rôle important dans la prolongation de la durée de vie des équipements et dans l’amélioration de l’efficacité opérationnelle.
La maintenance corrective présente plusieurs avantages significatifs. Premièrement, elle permet de réduire les risques de pannes majeures et les temps d’arrêt non planifiés, ce qui peut avoir un impact direct sur la productivité et la rentabilité d’une entreprise. En identifiant et en traitant les problèmes avant qu’ils ne deviennent critiques, les entreprises peuvent mieux planifier les interventions de maintenance, minimisant ainsi les perturbations dans leurs opérations quotidiennes. Deuxièmement, cette approche contribue à une meilleure gestion des ressources. En effectuant des réparations ciblées, les entreprises peuvent optimiser l’utilisation de leurs pièces de rechange et de leur main-d’œuvre, au lieu de recourir à des réparations d’urgence plus coûteuses et exigeantes en ressources. Cependant, la maintenance corrective comporte aussi des inconvénients. Elle nécessite une surveillance constante et des inspections régulières pour être efficace, ce qui peut entraîner des coûts supplémentaires en termes de temps et de main-d’œuvre. De plus, même si elle est plus proactive que la maintenance curative, elle reste une approche réactive dans une certaine mesure, car elle dépend de la détection des problèmes, qui peuvent parfois être subtils ou difficiles à identifier avant qu’ils ne s’aggravent. Enfin, la dépendance à la maintenance corrective sans une stratégie globale de maintenance préventive ou prédictive peut conduire à une vision fragmentée de la santé globale des équipements, risquant ainsi de manquer des opportunités d’optimisation et d’amélioration continue.
La maintenance prédictive
La maintenance prédictive représente une approche révolutionnaire dans la gestion de la maintenance industrielle. Elle repose sur l’utilisation de technologies avancées, comme l’analyse des données, l’intelligence artificielle (IA) et l’Internet des Objets (IoT), pour prévoir les pannes avant qu’elles ne surviennent. Cette stratégie implique une surveillance continue et l’analyse des données de performance des équipements en temps réel. Par exemple, des capteurs placés sur les machines collectent des données sur des paramètres tels que les vibrations, la température, ou la consommation d’énergie. Ces données sont ensuite analysées pour détecter les tendances ou les anomalies qui pourraient indiquer un risque de défaillance future. La maintenance prédictive permet ainsi d’intervenir de manière proactive pour effectuer des réparations ou des remplacements avant que les équipements ne tombent en panne, optimisant les périodes de maintenance et réduisant les interruptions inattendues de la production. Cette approche augmente la durée de vie des équipements et améliore l’efficacité globale des opérations en minimisant les coûts et les pertes associés aux pannes. La maintenance prédictive est particulièrement bénéfique dans les industries où les équipements sont soumis à de fortes contraintes ou où les arrêts de production ont un impact économique important.
La maintenance prédictive transforme l’industrie de plusieurs manières significatives. D’abord, elle améliore considérablement la fiabilité et la disponibilité des équipements. En anticipant les problèmes avant qu’ils ne se manifestent, les entreprises peuvent planifier les interventions de maintenance de manière plus efficace, évitant ainsi les arrêts de production non planifiés qui sont coûteux et perturbateurs. De plus, cette approche permet une utilisation plus rationnelle des ressources de maintenance. Plutôt que de suivre un calendrier de maintenance rigide ou de réagir aux pannes, les entreprises peuvent allouer leur main-d’œuvre et leurs pièces de rechange de manière plus stratégique, en fonction des besoins réels identifiés par l’analyse prédictive. Cela conduit à une optimisation des coûts et à une meilleure allocation des ressources.
En outre, la maintenance prédictive joue un rôle crucial dans l’intégration des technologies numériques dans le secteur industriel. L’utilisation de l’IA, de l’analyse de données et de l’IoT offre des possibilités inédites pour la collecte et l’analyse de données à grande échelle, permettant ainsi une meilleure compréhension des performances et de la santé des équipements. Cette transformation numérique ouvre la voie à des usines plus intelligentes et plus connectées, où les décisions de maintenance sont basées sur des données précises et en temps réel, plutôt que sur des estimations ou des routines préétablies. Finalement, la maintenance prédictive contribue à une culture d’amélioration continue dans les entreprises, où les informations tirées de l’analyse des données sont utilisées pour optimiser en permanence les processus de production et de maintenance, conduisant à une efficacité opérationnelle accrue et à une compétitivité renforcée sur le marché.
La maintenance préventive systématique
La maintenance préventive systématique est une méthode stratégique dans la gestion des équipements industriels, caractérisée par la réalisation régulière et planifiée d’opérations de maintenance, indépendamment de l’état actuel des machines. Cette approche repose sur un calendrier prédéfini, basé sur le temps ou sur l’utilisation des équipements, pour effectuer des contrôles, des entretiens, des nettoyages, et des remplacements de pièces. Par exemple, une machine pourrait être soumise à une maintenance préventive tous les six mois ou après un certain nombre d’heures de fonctionnement. L’objectif principal de cette méthode est de prévenir les défaillances avant qu’elles ne se produisent, en maintenant les équipements dans un état optimal de fonctionnement. Cela contribue à réduire les risques de pannes inattendues et à prolonger la durée de vie des machines. De plus, la maintenance préventive systématique permet une meilleure planification des ressources et des coûts de maintenance, puisque les interventions sont programmées et prévisibles. Elle est particulièrement efficace pour les équipements dont le risque de défaillance augmente avec le temps ou l’utilisation, et où les coûts de maintenance préventive sont inférieurs aux coûts associés à une panne majeure. Cependant, cette approche peut parfois conduire à une maintenance excessive, où des pièces sont remplacées ou des services sont effectués plus fréquemment que nécessaire, ce qui peut entraîner une augmentation des coûts de maintenance à long terme.
Le rôle de la maintenance préventive systématique dans la prévention des pannes est crucial pour assurer la continuité et l’efficacité des opérations industrielles. En effectuant régulièrement des tâches de maintenance, les entreprises peuvent identifier et résoudre les problèmes potentiels avant qu’ils ne se transforment en défaillances majeures. Cette approche proactive aide à maintenir un haut niveau de fiabilité et de disponibilité des équipements, ce qui est essentiel pour les industries où les interruptions de production peuvent avoir des répercussions financières importantes. Par exemple, dans une chaîne de production, l’entretien régulier des composants critiques, comme les moteurs, les pompes et les systèmes de contrôle, peut prévenir des arrêts inattendus et coûteux. De plus, la maintenance préventive systématique contribue à une meilleure qualité de production, car les équipements bien entretenus sont moins susceptibles de produire des défauts ou des erreurs. Elle permet également une meilleure gestion des stocks de pièces de rechange, car les besoins de maintenance sont prévisibles et peuvent être planifiés à l’avance.
En outre, cette méthode de maintenance favorise une culture d’entretien et de soin régulier des équipements, ce qui peut avoir un impact positif sur la sensibilisation et l’engagement du personnel en matière de maintenance. En impliquant régulièrement les opérateurs et les techniciens dans les routines de maintenance, les entreprises peuvent renforcer la connaissance et la compréhension des équipements parmi leurs employés, ce qui contribue à une détection plus rapide des problèmes et à une résolution plus efficace. Enfin, la maintenance préventive systématique est un élément clé pour assurer la conformité aux normes de sécurité et réglementaires, en garantissant que les équipements sont toujours dans un état de fonctionnement sûr et fiable.
La maintenance préventive conditionnelle
Le marché de l’emploi dans la maintenance industrielle est influencé par plusieurs tendances actuelles. L’une des plus significatives est l’impact de la digitalisation et de l’automatisation sur les compétences requises. Avec l’intégration croissante de technologies avancées comme l’IoT, l’IA et la robotique, la demande pour des compétences en analyse de données, programmation et cybersécurité est en hausse. En parallèle, la mondialisation et la compétitivité accrue des marchés poussent les entreprises à optimiser l’efficacité et la fiabilité de leurs équipements, renforçant ainsi le besoin de professionnels hautement qualifiés en maintenance. Une autre tendance notable est l’accent mis sur la durabilité et l’efficacité énergétique, ce qui nécessite une expertise dans des domaines tels que la maintenance éco-responsable et l’optimisation des ressources. Ces tendances créent de nouvelles opportunités de carrière et exigent une mise à jour continue des compétences pour rester pertinents dans ce domaine dynamique.
Les perspectives d’emploi dans la maintenance industrielle sont prometteuses, en grande partie grâce à la nécessité constante d’entretien et d’amélioration des infrastructures et des équipements industriels. Les rôles varient de techniciens de terrain à ingénieurs de maintenance, avec des opportunités dans divers secteurs tels que la fabrication, l’énergie, l’aérospatiale et le transport. La demande pour des compétences spécialisées, en particulier celles liées aux nouvelles technologies, est en croissance, offrant des opportunités pour des carrières enrichissantes avec des possibilités de développement professionnel continu. En outre, la nature essentielle de la maintenance industrielle offre une certaine stabilité d’emploi, même en période de ralentissement économique. Les professionnels qui se concentrent sur l’acquisition et la mise à jour de leurs compétences, en particulier dans les domaines de la technologie et de la gestion de projet, peuvent s’attendre à une forte demande pour leurs services.
Les rôles dans la maintenance industrielle évoluent en réponse aux changements technologiques et aux exigences du marché. Les professionnels doivent désormais posséder une combinaison de compétences techniques, de capacités analytiques et de compétences en gestion. Les techniciens de maintenance ne se contentent plus de réparations et d’entretiens de routine ; ils sont également impliqués dans la planification stratégique, la gestion des données et la prise de décision basée sur des analyses prédictives. Le rôle de l’ingénieur de maintenance s’est également élargi, englobant désormais la gestion de projet, l’amélioration continue et l’innovation. Cette évolution nécessite une formation continue et une adaptabilité aux nouvelles méthodes de travail et technologies. En outre, avec l’accent mis sur la durabilité et l’efficacité, les professionnels de la maintenance jouent un rôle clé dans la mise en œuvre de pratiques éco-responsables et dans la contribution aux objectifs de durabilité des entreprises. Cette évolution des rôles reflète la nature dynamique du secteur et offre des opportunités stimulantes pour les professionnels engagés dans une carrière en maintenance industrielle.
Comparaison entre les types de maintenance
La comparaison entre les différents types de maintenance industrielle – curative, corrective, prédictive, préventive systématique et préventive conditionnelle – révèle des approches variées, chacune adaptée à des besoins spécifiques et offrant des avantages distincts. La maintenance curative, intervenant après une panne, est essentielle pour des réparations d’urgence mais peut entraîner des coûts élevés et des interruptions de production imprévues. La maintenance corrective, qui corrige les défauts avant qu’ils ne causent des pannes majeures, permet une meilleure planification et réduit les temps d’arrêt, bien qu’elle nécessite une surveillance et des inspections régulières. D’autre part, la maintenance prédictive, basée sur l’analyse des données et l’utilisation de technologies avancées, anticipe les défaillances avant leur survenue, optimisant la planification des maintenances et améliorant la durée de vie des équipements. Cependant, cette approche peut nécessiter des investissements initiaux importants en technologie et en formation. La maintenance préventive systématique, effectuée à intervalles réguliers, assure la fiabilité des équipements mais peut parfois conduire à une maintenance excessive. Enfin, la maintenance préventive conditionnelle, qui s’appuie sur l’état actuel des équipements, offre une optimisation des ressources en évitant les interventions inutiles, mais nécessite des systèmes de surveillance avancés. Chaque type de maintenance présente donc ses propres atouts et contraintes, et le choix de la méthode appropriée dépend de divers facteurs tels que le type d’équipement, l’environnement opérationnel, les ressources disponibles et les objectifs spécifiques de l’entreprise. Une stratégie de maintenance efficace implique souvent une combinaison de ces différentes approches, permettant ainsi une gestion optimale des équipements industriels.
Études de cas
Les études de cas dans le domaine de la maintenance industrielle illustrent comment différentes stratégies de maintenance sont appliquées dans des contextes réels, mettant en lumière leur efficacité et leurs impacts sur les opérations industrielles.
Un exemple concret de la maintenance prédictive peut être observé dans l’industrie aéronautique. Les compagnies aériennes utilisent des systèmes avancés de surveillance pour collecter des données en temps réel sur l’état de leurs avions. Grâce à l’analyse de ces données, telles que les vibrations des moteurs ou les conditions de vol, il est possible de prédire les besoins de maintenance avant que des problèmes ne se manifestent. Cela permet de planifier les interventions de maintenance de manière plus efficace, réduisant ainsi les retards et annulations de vols, tout en assurant la sécurité et la fiabilité des avions.
Dans le secteur de l’énergie, notamment dans les parcs éoliens, la maintenance préventive conditionnelle joue un rôle crucial. Des capteurs installés sur les éoliennes surveillent en continu divers paramètres tels que la vitesse du vent, les vibrations et la température. Lorsque les données indiquent une anomalie, comme une augmentation inhabituelle des vibrations, une intervention de maintenance est planifiée pour résoudre le problème avant qu’une panne ne survienne. Cela permet d’éviter des arrêts prolongés et coûteux des turbines, maximisant ainsi la production d’énergie et la rentabilité du parc éolien.
Un autre exemple se trouve dans l’industrie manufacturière, où la maintenance préventive systématique est couramment utilisée. Dans une usine automobile, par exemple, les robots de soudure et les chaînes de montage sont soumis à des vérifications et des entretiens réguliers, selon un calendrier prédéfini. Cette approche assure que les équipements fonctionnent de manière optimale et prévient les arrêts de production inattendus, qui pourraient entraîner des retards dans la livraison des véhicules et des pertes financières.
Ces exemples démontrent comment les différentes stratégies de maintenance peuvent être adaptées à des secteurs spécifiques, en tenant compte de la nature des équipements, des exigences de production et des objectifs de l’entreprise. Ils soulignent également l’importance d’une approche stratégique et réfléchie de la maintenance industrielle, qui non seulement assure le bon fonctionnement des équipements mais contribue également à la rentabilité et à la compétitivité à long terme des entreprises.
Les défis de la maintenance industrielle
La maintenance industrielle fait face à de multiples défis dans le contexte actuel, caractérisé par une technologie en constante évolution et des exigences de production de plus en plus élevées. Un des principaux défis est l’intégration des nouvelles technologies, comme l’Internet des Objets (IoT), l’intelligence artificielle (IA), et la robotique, dans les stratégies de maintenance existantes. Cette intégration requiert non seulement des investissements financiers importants mais aussi une formation continue du personnel pour maîtriser ces nouvelles technologies. De plus, la gestion des grandes quantités de données générées par ces technologies représente un défi en soi, nécessitant des systèmes de traitement et d’analyse de données sophistiqués pour en tirer des informations utiles et fiables pour la maintenance.
Un autre défi majeur est la nécessité d’assurer une maintenance efficace tout en minimisant les interruptions de production. Dans des secteurs où chaque minute d’arrêt peut engendrer des pertes considérables, il est crucial de planifier et d’exécuter la maintenance de manière à réduire au maximum les impacts sur la production. Cela implique souvent de trouver un équilibre entre les différents types de maintenance – préventive, prédictive, corrective et curative – pour garantir la fiabilité et la disponibilité des équipements sans compromettre la productivité. Par ailleurs, la maintenance doit également répondre aux normes de sécurité et environnementales de plus en plus strictes, ce qui requiert une veille réglementaire constante et des ajustements périodiques des pratiques de maintenance.
Face à ces défis, des solutions innovantes sont constamment développées et mises en œuvre. L’une des solutions les plus prometteuses est l’utilisation accrue de l’IA et de l’apprentissage automatique pour analyser les données issues des capteurs et des systèmes de surveillance. Ces technologies permettent de détecter des tendances et des anomalies qui pourraient indiquer un besoin de maintenance avant que des problèmes majeurs ne surviennent, facilitant ainsi une approche prédictive et proactive. En outre, l’adoption de l’IoT dans les pratiques de maintenance offre une surveillance en temps réel des équipements, améliorant la précision et l’efficacité des opérations de maintenance.
La digitalisation des processus de maintenance est une autre solution clé. L’utilisation de plateformes de gestion de maintenance assistée par ordinateur (GMAO) permet une meilleure planification, suivi, et analyse des activités de maintenance, ainsi qu’une gestion optimisée des stocks de pièces de rechange. Ces systèmes contribuent à réduire les coûts et à améliorer la productivité en fournissant des informations précises et en temps réel sur l’état des équipements et des opérations de maintenance.
Enfin, la formation continue et le développement des compétences du personnel de maintenance sont essentiels pour s’adapter aux évolutions technologiques et aux méthodes de maintenance modernes. Investir dans la formation et le développement des compétences garantit que les équipes de maintenance sont bien équipées pour gérer les équipements complexes et tirer pleinement parti des technologies avancées. Ces solutions innovantes, combinées à une stratégie de maintenance bien conçue, sont essentielles pour relever les défis actuels de la maintenance industrielle et assurer la durabilité et l’efficacité des opérations industrielles.
L’avenir de la maintenance industrielle
L’avenir de la maintenance industrielle se profile sous le signe de l’innovation technologique et de l’optimisation des processus. Avec l’avènement de l’industrie 4.0, on s’attend à une intégration encore plus poussée des technologies numériques, telles que l’Internet des Objets (IoT), l’intelligence artificielle (IA), la réalité augmentée et la robotique, dans les stratégies de maintenance. Ces technologies vont permettre une surveillance et une analyse en temps réel des équipements, conduisant à une maintenance de plus en plus prédictive et moins réactive. L’IA, en particulier, jouera un rôle crucial dans l’analyse des données massives générées par les capteurs pour prédire précisément les besoins de maintenance, réduisant ainsi les temps d’arrêt et augmentant la durée de vie des équipements. On assistera également à une personnalisation accrue des stratégies de maintenance, où les solutions seront adaptées spécifiquement aux besoins et au contexte de chaque entreprise. La durabilité sera un autre aspect important, avec une attention croissante portée à l’efficacité énergétique et à la réduction de l’empreinte écologique dans les pratiques de maintenance. La formation et le développement des compétences du personnel resteront essentiels pour s’adapter aux changements technologiques. L’intégration de systèmes de formation virtuelle et de simulation pourraient devenir courants, permettant aux techniciens de se former efficacement sur des équipements complexes dans un environnement sûr et contrôlé. En somme, l’avenir de la maintenance industrielle sera caractérisé par une convergence entre technologie de pointe et compétences humaines, visant une efficacité opérationnelle maximale, une fiabilité accrue des équipements et une meilleure durabilité globale.
À retenir
Dans le domaine de la maintenance industrielle, plusieurs éléments clés doivent être retenus pour assurer l’efficacité et la pérennité des opérations. Tout d’abord, l’importance de choisir la stratégie de maintenance appropriée en fonction du contexte spécifique de chaque entreprise est primordiale. Que ce soit la maintenance curative, corrective, préventive systématique, préventive conditionnelle ou prédictive, chaque type a son rôle spécifique et contribue de manière unique à la performance globale des équipements. La maintenance curative et corrective sont essentielles pour les interventions rapides et efficaces, tandis que les approches préventives et prédictives jouent un rôle crucial dans la prévention des pannes et la réduction des temps d’arrêt.
L’intégration des technologies avancées comme l’IA, l’IoT et l’analyse de données est un autre élément fondamental. Ces technologies permettent une meilleure anticipation des problèmes, une optimisation des interventions de maintenance et une plus grande efficacité opérationnelle. Elles offrent aussi l’avantage d’une meilleure gestion des ressources et d’une réduction des coûts à long terme.
La formation continue du personnel de maintenance est également essentielle. Avec l’évolution rapide des technologies, la mise à jour des compétences et la compréhension approfondie des systèmes modernes de maintenance sont indispensables pour maintenir une efficacité maximale.
Enfin, l’importance de la durabilité dans les pratiques de maintenance est de plus en plus reconnue. Cela implique non seulement de veiller à l’efficacité énergétique et à la réduction de l’empreinte écologique des opérations de maintenance, mais aussi de s’assurer que les équipements sont maintenus de manière à prolonger leur durée de vie et à réduire le besoin de remplacements fréquents.
En somme, ces éléments à retenir mettent en lumière la complexité et l’importance stratégique de la maintenance industrielle dans le monde moderne. Ils soulignent le besoin d’une approche holistique qui combine technologie, compétence humaine et considérations environnementales pour une industrie plus efficace, fiable et durable.
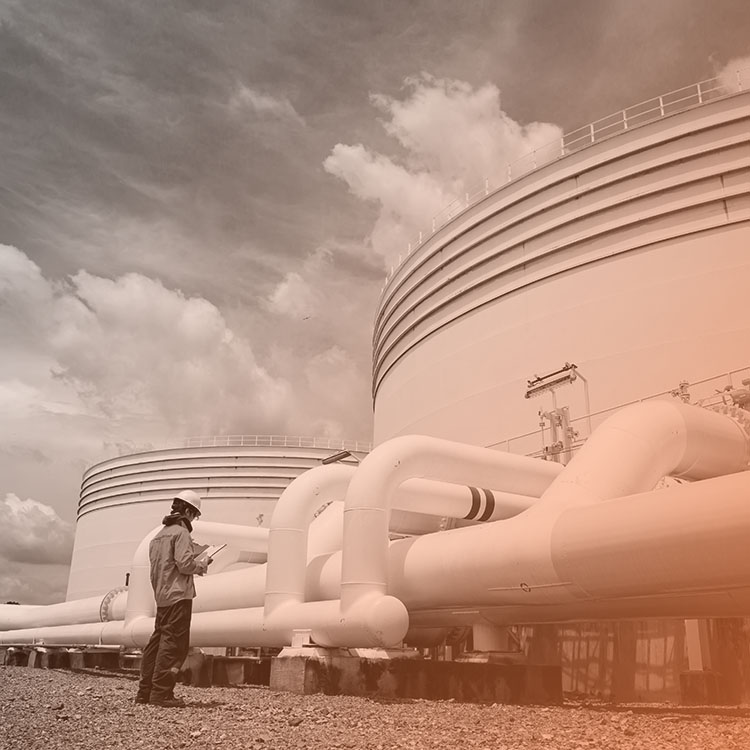
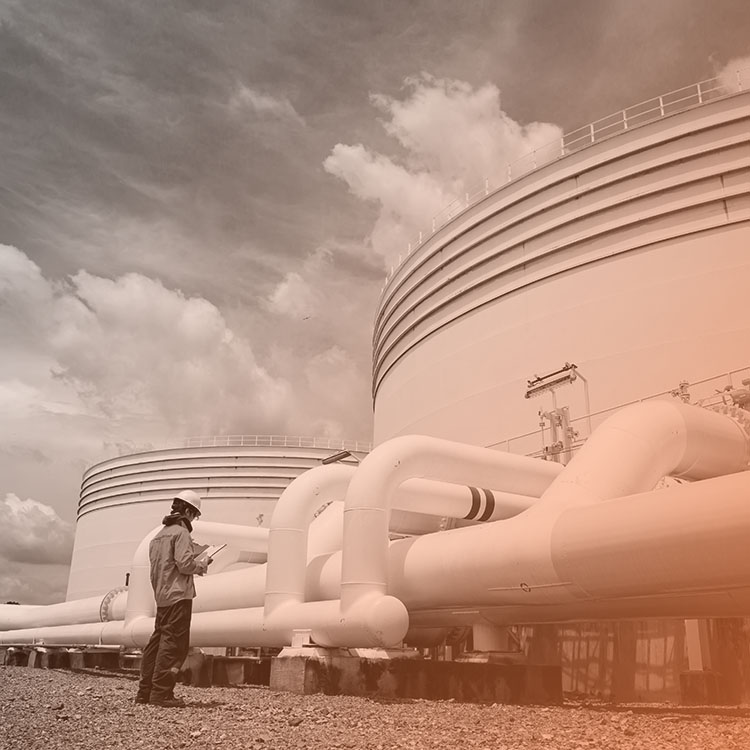
Nos offres
Simplifiez la gestion
de votre infrastructure
Notre plus grande fierté
Plus de 120 clients satisfaits:
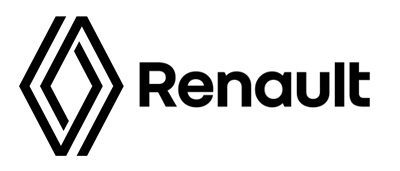
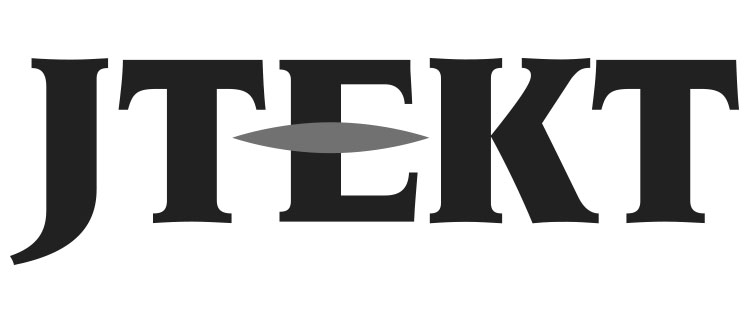
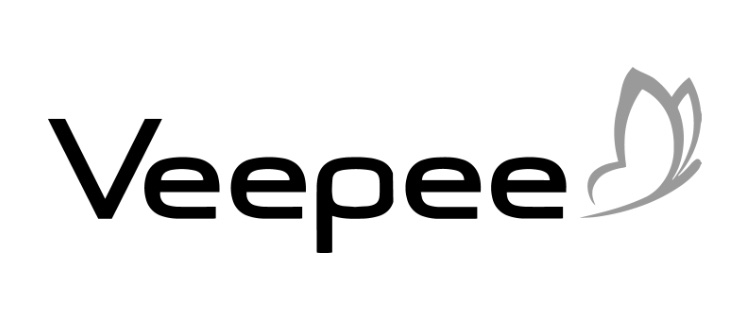
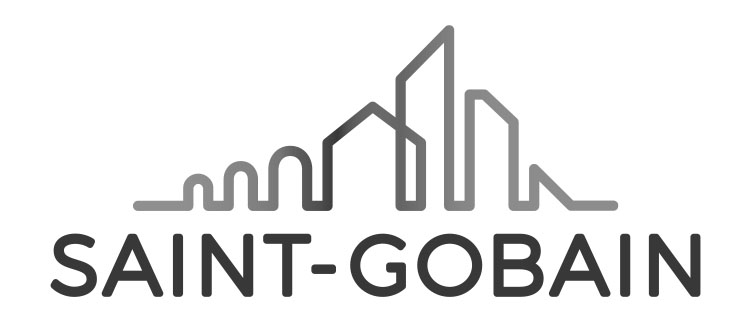
5
agences en France
8.3 M€
prévisionnel CA 2024
120
clients réguliers
24h
délai d’intervention
100