Comparatif Économique : La Maintenance Prédictive est-elle Plus Avantageuse que la Corrective ?
La maintenance prédictive représente une approche proactive dans la gestion et l’entretien des équipements industriels. Son objectif principal est d’anticiper les pannes et les dysfonctionnements avant qu’ils ne surviennent, afin de maintenir un fonctionnement optimal des machines et d’éviter des arrêts imprévus. Cette méthode s’appuie sur l’utilisation de technologies avancées telles que l’analyse de données, l’intelligence artificielle, et l’Internet des Objets (IoT) pour surveiller en temps réel l’état des équipements. En analysant les tendances et les modèles de performance, la maintenance prédictive permet d’identifier les signaux d’alerte précoces de défaillance potentielle. Par exemple, en surveillant les vibrations, la température, et d’autres paramètres clés, il est possible de détecter des anomalies qui, si traitées à temps, peuvent prévenir des dommages plus importants. Cette approche nécessite non seulement une technologie avancée mais également une compétence analytique pour interpréter correctement les données recueillies, ce qui en fait une stratégie à la fois sophistiquée et hautement efficace pour la gestion des équipements industriels.
Contrairement à la maintenance prédictive, la maintenance corrective intervient après qu’une défaillance ou un dysfonctionnement se soit produit. Cette méthode est traditionnellement réactive, c’est-à-dire qu’elle répond à un problème après son apparition. Le processus de maintenance corrective peut varier en complexité, allant de réparations mineures à des remplacements complets de pièces ou de systèmes. Cette approche est souvent moins coûteuse en termes d’investissement initial par rapport à la maintenance prédictive, car elle ne nécessite pas de technologies avancées pour la surveillance continue. Cependant, elle peut entraîner des coûts plus élevés à long terme en raison d’arrêts de production non planifiés et de réparations d’urgence. De plus, la maintenance corrective ne prévient pas les pannes mais se contente de les traiter une fois qu’elles se sont produites, ce qui peut entraîner une usure plus rapide des équipements et une diminution de leur durée de vie. Dans certains cas, une maintenance corrective régulière peut être planifiée suite à des inspections périodiques, mais en général, elle est souvent perçue comme une solution moins idéale en termes de gestion proactive des équipements.
Histoire et évolution de la maintenance
L’histoire de la maintenance remonte à l’époque où les premières machines et équipements industriels ont été créés. À cette époque, la maintenance était principalement réactive, c’est-à-dire qu’elle intervenait uniquement en cas de panne ou de dysfonctionnement. Cette approche, souvent qualifiée de maintenance corrective, reposait sur l’idée simple de réparer ce qui était cassé. Au fur et à mesure que l’industrie et la technologie évoluaient, la nécessité d’améliorer l’efficacité et de réduire les temps d’arrêt est devenue évidente. Cette prise de conscience a conduit à l’émergence de méthodes de maintenance plus structurées et planifiées. Au début, ces méthodes se concentraient sur des inspections régulières et des entretiens préventifs pour éviter les pannes. Avec l’avènement de la révolution industrielle, l’importance de la maintenance est devenue encore plus cruciale à mesure que les machines devenaient plus complexes et que les processus de production s’intensifiaient. Cette période a marqué un tournant décisif dans la manière dont la maintenance était perçue et gérée, posant les fondements des pratiques modernes de maintenance prédictive et proactive.
L’évolution vers des approches modernes de maintenance a été largement influencée par les progrès technologiques et l’innovation industrielle. L’intégration de l’électronique et de l’informatique dans les équipements industriels a permis le développement de systèmes de surveillance et de diagnostic plus avancés. Ces technologies ont ouvert la voie à la maintenance prédictive, où les données recueillies par divers capteurs permettent de prévoir les pannes avant qu’elles ne surviennent. L’utilisation de l’intelligence artificielle et de l’apprentissage automatique pour analyser ces données a encore amélioré la précision et l’efficacité de ces prédictions. Parallèlement, la gestion de la maintenance est devenue plus intégrée et stratégique. Les entreprises ont commencé à reconnaître que la maintenance ne devait pas seulement être considérée comme un coût nécessaire, mais plutôt comme un élément clé contribuant à la performance globale, à l’efficacité et à la durabilité de leurs opérations. Cette perspective holistique a encouragé l’adoption d’approches de maintenance plus complètes et intégrées, telles que la maintenance centrée sur la fiabilité (RCM) et la gestion totale de la maintenance productive (TPM), qui visent à optimiser la disponibilité et la performance des équipements tout en minimisant les coûts et les risques.
Principes de la maintenance prédictive
La maintenance prédictive s’appuie sur une gamme de technologies avancées pour surveiller et diagnostiquer l’état des équipements industriels. Au cœur de cette approche se trouvent les systèmes de surveillance basés sur l’Internet des Objets (IoT), qui permettent une collecte de données en temps réel sur l’état de fonctionnement des machines. Ces données peuvent inclure des mesures de vibration, de température, de pression, et d’autres indicateurs critiques. L’analyse de ces données est ensuite effectuée en utilisant des logiciels sophistiqués qui intègrent l’intelligence artificielle (IA) et l’apprentissage automatique. Ces outils sont capables de détecter des modèles et des anomalies qui préfigurent souvent des défaillances. En outre, les systèmes de vision industrielle et les capteurs acoustiques jouent également un rôle important en fournissant des informations supplémentaires sur l’état des machines. Grâce à ces technologies, la maintenance prédictive peut non seulement identifier les problèmes potentiels bien avant qu’ils ne se manifestent, mais aussi recommander des actions de maintenance spécifiques pour prévenir les pannes. Cette approche technologique rend la maintenance prédictive extrêmement efficace pour prolonger la durée de vie des équipements, optimiser la performance, et réduire les coûts d’exploitation à long terme.
Les avantages de la maintenance prédictive sont multiples et significatifs, en particulier en termes d’efficacité opérationnelle et de réduction des coûts. Tout d’abord, cette approche permet d’anticiper les pannes, ce qui réduit considérablement les arrêts non planifiés et augmente la disponibilité des équipements. En prévoyant les besoins de maintenance, les entreprises peuvent planifier les interventions de manière plus efficace, en évitant les interruptions imprévues qui perturbent la production. Cela entraîne une augmentation de la productivité et une meilleure utilisation des ressources. De plus, la maintenance prédictive contribue à prolonger la durée de vie des équipements en traitant les problèmes avant qu’ils ne deviennent graves. Cela signifie une réduction des coûts liés au remplacement des équipements et une meilleure rentabilisation des investissements initiaux. Sur le plan financier, bien que l’installation de systèmes de maintenance prédictive représente un investissement initial, les économies réalisées en termes de réductions des pannes et d’amélioration de l’efficacité compensent largement ce coût sur le long terme. Enfin, cette approche améliore également la sécurité des opérations en réduisant les risques de défaillances majeures qui pourraient mettre en danger les employés et l’environnement de travail.
Principes de la maintenance corrective
La maintenance corrective est généralement mise en œuvre dans des scénarios où les équipements subissent une défaillance ou un dysfonctionnement imprévu. Contrairement à la maintenance prédictive, qui se base sur l’anticipation, la maintenance corrective est réactive et intervient après l’identification d’un problème. Les scénarios typiques incluent des pannes de machines, des défaillances de composants, ou des dysfonctionnements soudains qui affectent le processus de production. Dans de tels cas, des mesures immédiates sont nécessaires pour réparer ou remplacer les pièces défectueuses afin de rétablir la fonctionnalité de l’équipement. Cette approche peut varier de simples ajustements ou réparations mineures à des interventions plus complexes nécessitant un remplacement complet de pièces ou de systèmes. Un aspect clé de la maintenance corrective est sa nature imprévisible, ce qui peut entraîner des défis en termes de planification des ressources et de gestion des stocks de pièces de rechange. De plus, les interruptions non planifiées dans la production dues à des pannes inattendues peuvent avoir un impact significatif sur la productivité et les coûts opérationnels. La maintenance corrective est souvent vue comme une solution à court terme, nécessaire pour gérer des problèmes urgents, mais sans contribuer à une stratégie de maintenance globale axée sur la prévention et l’optimisation à long terme.
Malgré ses limites, la maintenance corrective présente plusieurs avantages, en particulier en termes de flexibilité et de coûts initiaux. Premièrement, cette méthode est souvent moins coûteuse en termes d’investissement initial par rapport à la maintenance prédictive, car elle ne requiert pas de technologies avancées pour la surveillance continue des équipements. Cela la rend accessible même pour les petites entreprises qui ne peuvent pas se permettre d’investir dans des systèmes de maintenance prédictive sophistiqués. De plus, la maintenance corrective peut être adaptée aux besoins spécifiques de chaque situation, permettant une approche plus personnalisée pour résoudre les problèmes. Dans certains cas, les réparations et ajustements effectués peuvent améliorer la performance des équipements ou prolonger leur durée de vie. Un autre avantage est la simplicité et la familiarité de cette approche pour de nombreux techniciens et ingénieurs de maintenance, qui sont souvent formés et expérimentés dans la résolution de problèmes survenant après une panne. Enfin, dans des environnements où les équipements ne sont pas critiques pour la continuité de la production ou dans des situations où les temps d’arrêt programmés sont acceptables, la maintenance corrective peut être une solution pratique et économique. Cependant, il est important de noter que la dépendance excessive à la maintenance corrective peut conduire à des coûts cachés à long terme, comme des arrêts de production fréquents et une usure accélérée des équipements.
Comparaison des coûts
Les coûts initiaux de la maintenance prédictive sont généralement plus élevés que ceux de la maintenance corrective. Cette différence est due à l’investissement nécessaire dans les technologies avancées telles que les capteurs, les logiciels d’analyse de données, et les systèmes intégrés de gestion de maintenance. La mise en place d’un système de maintenance prédictive implique non seulement l’achat de ces équipements mais aussi leur installation et la formation du personnel pour leur utilisation efficace. Ces coûts initiaux peuvent représenter un obstacle pour certaines entreprises, en particulier les petites et moyennes entreprises qui disposent de budgets limités. En revanche, la maintenance corrective présente des coûts initiaux relativement bas, car elle ne nécessite pas d’investissements technologiques conséquents. Les dépenses se concentrent principalement sur les outils de réparation et les pièces de rechange nécessaires pour les interventions ponctuelles. Cette approche est souvent perçue comme plus abordable à court terme, bien qu’elle puisse entraîner des coûts imprévus importants en cas de pannes majeures. La décision entre ces deux approches dépend donc des capacités financières de l’entreprise, de la nature de ses opérations et de sa stratégie à long terme en matière de maintenance.
Sur le long terme, les coûts de la maintenance prédictive tendent à être inférieurs à ceux de la maintenance corrective. Bien que l’investissement initial pour la mise en place de la maintenance prédictive soit plus élevé, les économies réalisées grâce à la réduction des pannes imprévues et des arrêts de production peuvent être substantielles. La capacité à anticiper et à prévenir les problèmes avant qu’ils ne surviennent aide à maintenir un fonctionnement fluide et efficace des équipements, réduisant ainsi les coûts liés aux interruptions d’activité et aux réparations d’urgence. De plus, en prolongeant la durée de vie des équipements, la maintenance prédictive contribue à diminuer les dépenses liées au remplacement de matériel. En revanche, bien que les coûts initiaux de la maintenance corrective soient plus faibles, cette approche peut entraîner des dépenses importantes à long terme. Les pannes non anticipées peuvent causer des interruptions coûteuses dans la production, sans compter les coûts associés aux réparations d’urgence et au remplacement fréquent des pièces. Ces coûts imprévus, cumulés au fil du temps, peuvent surpasser l’investissement initial requis pour la maintenance prédictive. Par conséquent, pour une planification financière à long terme, la maintenance prédictive peut s’avérer être une option plus économique, en particulier pour les entreprises dont les opérations dépendent fortement de la fiabilité et de la disponibilité des équipements.
Comparaison des bénéfices
L’efficacité opérationnelle de la maintenance prédictive est l’un de ses avantages les plus significatifs. Cette méthode permet une gestion proactive des équipements, réduisant les arrêts imprévus et maximisant la disponibilité des machines. En utilisant des données collectées en temps réel et analysées par des algorithmes avancés, la maintenance prédictive peut identifier avec précision les signes avant-coureurs de défaillance, permettant ainsi des interventions ciblées avant que les problèmes ne deviennent critiques. Cette approche assure une continuité dans les opérations de production, évitant les perturbations coûteuses et améliorant la productivité globale. De plus, en anticipant les besoins de maintenance, les entreprises peuvent mieux planifier leurs ressources, allouer le personnel de manière plus efficace, et gérer leur inventaire de pièces de rechange de manière optimale. Cette planification stratégique contribue à une meilleure organisation des flux de travail et à une utilisation plus efficiente des ressources. Par ailleurs, la maintenance prédictive peut également avoir un impact positif sur la qualité des produits finis, car les équipements maintenus de manière optimale sont moins susceptibles de connaître des défaillances qui pourraient compromettre la qualité. En somme, la maintenance prédictive favorise une performance opérationnelle améliorée, une meilleure fiabilité des équipements, et une efficacité accrue des processus de production.
La maintenance prédictive joue également un rôle important dans la promotion de la durabilité au sein des opérations industrielles. En prévenant les pannes et en optimisant l’utilisation des équipements, cette approche contribue à une utilisation plus efficace des ressources et à une réduction de la consommation d’énergie. En évitant les dysfonctionnements et les défaillances majeures, la maintenance prédictive réduit le besoin de remplacer fréquemment les équipements, ce qui a un impact positif sur la réduction des déchets et de la consommation de matières premières. De plus, en maintenant les machines à un niveau optimal de fonctionnement, la maintenance prédictive contribue à minimiser les émissions et les rejets nocifs, favorisant ainsi un environnement de travail plus sain et réduisant l’empreinte écologique de l’entreprise. Cette approche aligne donc les objectifs de performance industrielle avec ceux de la responsabilité environnementale, ce qui est de plus en plus important dans le contexte actuel de sensibilisation aux enjeux écologiques et de développement durable. La maintenance prédictive s’inscrit ainsi dans une vision à long terme de la gestion des opérations, où l’efficacité économique et la durabilité environnementale vont de pair, bénéficiant non seulement à l’entreprise mais également à la société dans son ensemble.
Cas pratiques: Maintenance prédictive
Dans le secteur industriel, la maintenance prédictive est de plus en plus adoptée grâce à ses nombreux avantages en termes d’efficacité et de réduction des coûts. Un exemple concret de son application se trouve dans l’industrie manufacturière, où des capteurs et des systèmes d’analyse des données sont utilisés pour surveiller l’état des équipements de production. Par exemple, dans une usine automobile, la maintenance prédictive permet de surveiller en continu les robots de montage et d’assemblage. Grâce à l’analyse des données de vibration et de température, il est possible de détecter les signes de défaillance des moteurs ou des composants mécaniques, permettant ainsi une intervention avant que ces problèmes n’entraînent des arrêts de production coûteux. Un autre exemple se trouve dans l’industrie énergétique, en particulier dans les centrales électriques, où la maintenance prédictive est utilisée pour surveiller les turbines et les générateurs. Les capteurs peuvent détecter des anomalies telles que des déséquilibres ou des surchauffes, permettant ainsi de réaliser des maintenances ciblées qui évitent des pannes majeures et prolongent la durée de vie des équipements. Ces exemples illustrent comment la maintenance prédictive améliore non seulement la fiabilité et la performance des équipements, mais contribue également à une meilleure planification des opérations et à une réduction des coûts d’entretien.
Les études de cas dans diverses industries démontrent l’efficacité de la maintenance prédictive. Par exemple, dans l’industrie aéronautique, l’utilisation de la maintenance prédictive pour surveiller les moteurs d’avion a conduit à une amélioration significative de la sécurité et de la fiabilité des vols. Les compagnies aériennes utilisent des systèmes sophistiqués pour collecter des données en temps réel sur la performance des moteurs durant les vols. Ces données, une fois analysées, permettent de prévoir les besoins de maintenance avant que des problèmes ne surviennent, réduisant ainsi les risques de défaillance en vol. Un autre cas concerne l’industrie ferroviaire, où la maintenance prédictive est appliquée pour surveiller l’état des rails et des trains. Des capteurs placés sur les rails et les wagons collectent des données sur les conditions de fonctionnement, telles que les vibrations et les forces exercées. Ces informations permettent de détecter les signes de fatigue ou d’usure des composants, permettant ainsi une maintenance proactive pour garantir la sécurité et la ponctualité des services. Ces études de cas montrent que la maintenance prédictive ne se limite pas à améliorer l’efficacité opérationnelle, mais joue également un rôle crucial dans la prévention des accidents et l’amélioration de la sécurité dans divers secteurs industriels.
Cas pratiques: Maintenance corrective
Dans le cadre industriel, la maintenance corrective est souvent mise en œuvre dans des situations d’urgence ou suite à des défaillances imprévues des équipements. Par exemple, dans l’industrie de la métallurgie, les fours à haute température sont sujets à des défaillances soudaines dues à des contraintes thermiques extrêmes. Lorsqu’une telle défaillance se produit, une intervention corrective immédiate est nécessaire pour réparer ou remplacer les composants endommagés afin de minimiser les temps d’arrêt. Un autre exemple se trouve dans le secteur de la chimie, où les réacteurs et les systèmes de tuyauterie peuvent présenter des fuites ou des ruptures. Dans ces cas, la maintenance corrective doit être rapide et efficace pour éviter des conséquences plus graves, comme des arrêts de production ou des risques pour la sécurité. Ces exemples illustrent la nature réactive de la maintenance corrective, où l’accent est mis sur la résolution rapide des problèmes pour restaurer la fonctionnalité des équipements. Bien que cette approche puisse être efficace pour gérer des incidents spécifiques, elle peut conduire à des coûts plus élevés à long terme et à une diminution de la durée de vie des équipements en raison d’interventions fréquentes et parfois intensives.
Des études de cas dans divers secteurs illustrent les défis et les implications de la maintenance corrective. Par exemple, dans le secteur des transports publics, des pannes inattendues de bus ou de trains peuvent entraîner des interventions correctives urgentes. Ces situations nécessitent non seulement des réparations immédiates pour remettre les véhicules en service, mais elles peuvent également causer des perturbations significatives dans les horaires et la satisfaction des usagers. Un autre cas peut être observé dans les hôpitaux, où les équipements médicaux jouent un rôle vital. Une défaillance d’un appareil critique comme un respirateur exige une maintenance corrective immédiate pour assurer la continuité des soins aux patients. Ces cas mettent en évidence l’importance de la rapidité et de l’efficacité de la maintenance corrective dans des situations critiques. Cependant, ils soulignent également les limitations de cette approche, en particulier en termes de planification des ressources et de gestion des risques. En effet, la dépendance à la maintenance corrective peut conduire à des pressions accrues sur les équipes de maintenance et à des coûts imprévus, soulignant la nécessité d’une approche équilibrée qui intègre à la fois des éléments prédictifs et correctifs dans la stratégie globale de maintenance.
Risques et défis de la maintenance prédictive
La maintenance prédictive, malgré ses nombreux avantages, comporte une complexité technologique significative. L’implémentation de cette méthode nécessite non seulement des investissements en matériel avancé, tels que des capteurs et des systèmes d’analyse des données, mais aussi une expertise technique pour gérer et interpréter ces données. Les systèmes de maintenance prédictive reposent sur une multitude de technologies, comme l’Internet des Objets (IoT), l’intelligence artificielle (IA), et l’apprentissage automatique, qui requièrent des compétences spécialisées pour leur mise en œuvre et leur maintenance. La gestion de grandes quantités de données et leur analyse précise pour prédire les défaillances potentielles constituent un défi en soi. De plus, l’intégration de ces systèmes avec l’infrastructure existante et leur adaptation aux spécificités de chaque équipement nécessitent une planification et une coordination minutieuses. Cette complexité peut représenter un obstacle, en particulier pour les petites et moyennes entreprises qui ne disposent pas des ressources ou des compétences nécessaires en interne. Par ailleurs, la maintenance prédictive exige une mise à jour et une évolution constantes pour s’adapter aux nouvelles technologies et aux changements dans les conditions d’exploitation, ce qui implique un engagement continu en termes de temps et de ressources financières.
Un autre défi majeur de la maintenance prédictive est sa dépendance aux données. Pour que cette approche soit efficace, il est essentiel de disposer de données précises, complètes et fiables. La qualité des prédictions dépend directement de la qualité des données recueillies par les capteurs et des algorithmes utilisés pour leur analyse. Cela implique non seulement d’avoir des capteurs fonctionnant correctement et placés de manière optimale sur les équipements, mais aussi des systèmes capables de traiter et d’analyser d’importants volumes de données en temps réel. La gestion des données pose également des défis en termes de stockage, de sécurité et de confidentialité, en particulier dans des secteurs réglementés. De plus, la dépendance aux données peut rendre les systèmes vulnérables en cas de défaillances des capteurs ou de perturbations dans la collecte des données, ce qui peut conduire à des erreurs de diagnostic ou à des omissions dans la détection des problèmes. Par conséquent, bien que la maintenance prédictive offre de nombreux avantages, sa mise en œuvre réussie nécessite une gestion rigoureuse des données et une infrastructure technologique solide pour assurer l’exactitude et la fiabilité des prédictions.
Risques et défis de la maintenance corrective
La maintenance corrective, bien qu’essentielle dans de nombreux scénarios industriels, comporte des risques opérationnels significatifs. Le principal risque est lié à l’incertitude et à l’imprévisibilité des pannes, qui peuvent entraîner des arrêts non planifiés de la production. Ces interruptions soudaines peuvent avoir un impact majeur sur la continuité des opérations, entraînant des pertes de production et des coûts supplémentaires significatifs. De plus, les interventions de maintenance corrective sont souvent réalisées dans l’urgence, ce qui peut compromettre la qualité des réparations et augmenter le risque d’erreurs ou de défaillances secondaires. Cette situation est particulièrement problématique dans des secteurs où la fiabilité des équipements est cruciale, comme dans l’industrie pharmaceutique ou aéronautique. Par ailleurs, la maintenance corrective peut également entraîner une usure accélérée des équipements. Les réparations fréquentes ou les remplacements de pièces peuvent réduire la durée de vie des machines, entraînant des coûts de remplacement plus élevés à long terme. En outre, cette approche peut avoir un impact négatif sur la sécurité des opérateurs, en particulier si les défaillances de l’équipement surviennent de manière inattendue, créant des situations potentiellement dangereuses.
Un autre inconvénient majeur de la maintenance corrective est lié aux coûts imprévus qu’elle peut engendrer. Contrairement à la maintenance prédictive, qui permet une planification et une budgétisation plus précises, la maintenance corrective est souvent associée à des dépenses non planifiées dues aux pannes inattendues. Ces coûts peuvent être significatifs, en particulier si la panne affecte des équipements cruciaux ou si elle survient pendant des périodes de forte activité de production. Les coûts directs incluent non seulement les frais de réparation ou de remplacement des pièces endommagées, mais aussi les coûts indirects liés aux arrêts de production, à la perte de productivité, et parfois à la détérioration de la qualité des produits finis. De plus, la nature réactive de la maintenance corrective peut entraîner une gestion moins efficace des ressources humaines et matérielles. Les équipes de maintenance peuvent se retrouver sous pression, avec des charges de travail imprévisibles et des délais serrés pour les réparations. Cette situation peut affecter la planification à long terme et la répartition des ressources, rendant la gestion globale de la maintenance plus complexe et potentiellement moins efficace. En somme, bien que la maintenance corrective soit indispensable dans certaines situations, elle présente des défis en termes de gestion des risques opérationnels et de maîtrise des coûts, soulignant l’importance d’une approche équilibrée qui intègre les avantages de la maintenance prédictive.
L’avenir de la maintenance dans l’industrie
L’avenir de la maintenance dans l’industrie est fortement marqué par les innovations technologiques. L’une des tendances les plus prometteuses est l’intégration accrue de l’intelligence artificielle (IA) et de l’apprentissage automatique dans les systèmes de maintenance prédictive. Ces technologies permettent une analyse plus fine et plus rapide des données collectées, offrant des prévisions de pannes plus précises et une optimisation de la planification de la maintenance. Par exemple, l’IA peut identifier des modèles complexes et des anomalies subtiles dans le comportement des machines, qui seraient difficiles à détecter par des méthodes traditionnelles. Une autre innovation importante est l’utilisation croissante de la réalité augmentée (RA) et de la réalité virtuelle (RV) pour la formation des techniciens de maintenance et l’assistance à distance. Ces technologies permettent aux techniciens de visualiser les problèmes en temps réel et de recevoir des instructions détaillées pour les réparations, améliorant ainsi l’efficacité et la précision des interventions. De plus, l’essor de l’Internet des Objets Industriel (IIoT) connecte les équipements à un réseau plus vaste, facilitant la collecte de données et permettant une surveillance continue et automatisée. Ces avancées technologiques transforment la maintenance d’une fonction réactive à une fonction stratégique, contribuant à une meilleure performance globale des entreprises.
Les perspectives d’avenir pour la maintenance dans l’industrie s’orientent vers une approche plus intégrée et stratégique. Avec l’évolution des technologies et l’accent croissant mis sur la durabilité et l’efficacité énergétique, la maintenance joue un rôle clé dans l’atteinte de ces objectifs. On s’attend à ce que les entreprises adoptent une approche holistique de la maintenance, combinant la maintenance prédictive, corrective et proactive pour optimiser la durée de vie et l’efficacité des équipements. Cette approche intégrée permettrait non seulement de réduire les coûts à long terme, mais aussi de minimiser l’impact environnemental des opérations industrielles. Par ailleurs, l’accent sera mis sur la formation et le développement des compétences des techniciens de maintenance pour qu’ils puissent gérer efficacement les technologies émergentes. L’importance croissante des données dans la prise de décision en matière de maintenance exigera également des compétences en analyse de données et en gestion de l’information. Enfin, la collaboration entre les fabricants d’équipements, les fournisseurs de technologie et les entreprises utilisatrices sera essentielle pour développer des solutions de maintenance innovantes et personnalisées. Cette collaboration intersectorielle pourrait conduire à de nouvelles méthodologies de maintenance, augmentant ainsi la fiabilité, la sécurité et l’efficacité des processus industriels.
À retenir
La comparaison entre la maintenance prédictive et la maintenance corrective dans l’industrie révèle des différences fondamentales en termes de coûts, d’efficacité, et d’impact à long terme.
Maintenance prédictive : Elle se caractérise par un investissement initial plus important, nécessaire pour l’acquisition et l’installation de technologies avancées telles que des capteurs et des systèmes d’analyse de données. Cependant, les coûts à long terme sont généralement inférieurs grâce à la réduction des pannes imprévues et des interruptions de production. Cette méthode, en anticipant les défaillances, permet une meilleure planification des ressources, une optimisation de la durée de vie des équipements, et une amélioration de la productivité. Les innovations technologiques, notamment l’IA, la RA et l’IIoT, jouent un rôle clé dans l’évolution de la maintenance prédictive, la rendant plus précise et efficace.
Maintenance corrective : Cette approche est souvent moins onéreuse en termes de coûts initiaux, mais peut entraîner des dépenses imprévues à long terme. Les interventions sont effectuées après la survenue des pannes, ce qui peut causer des arrêts de production et des réparations d’urgence coûteuses. Bien que la maintenance corrective soit indispensable dans certaines situations, elle présente des risques opérationnels et des coûts cachés, notamment en termes d’usure accélérée des équipements et de gestion moins efficace des ressources.
Comparaison des coûts et bénéfices : La maintenance prédictive, malgré un coût initial plus élevé, tend à être plus économique à long terme grâce à la réduction des arrêts non planifiés et à l’augmentation de la durée de vie des équipements. La maintenance corrective, quant à elle, peut sembler plus abordable à court terme, mais ses coûts imprévus et les perturbations qu’elle engendre peuvent s’avérer onéreux.
Perspectives d’avenir : L’industrie s’oriente vers une approche de maintenance plus intégrée, combinant les avantages de la maintenance prédictive et corrective. Les innovations technologiques continuent de jouer un rôle crucial dans ce domaine, améliorant la précision, la sécurité et l’efficacité des opérations de maintenance. La formation et le développement des compétences techniques sont essentiels pour gérer efficacement ces technologies.
En conclusion, la maintenance prédictive offre des avantages significatifs en termes de réduction des coûts à long terme, d’efficacité opérationnelle et de durabilité. Cependant, la maintenance corrective reste une composante essentielle dans la gestion des équipements industriels, soulignant l’importance d’une stratégie de maintenance équilibrée et intégrée pour les entreprises.
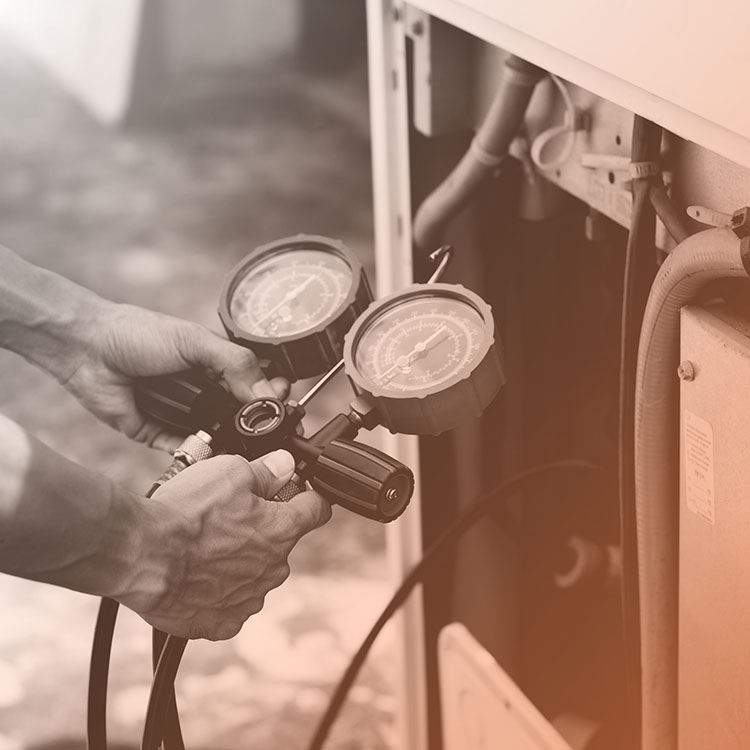
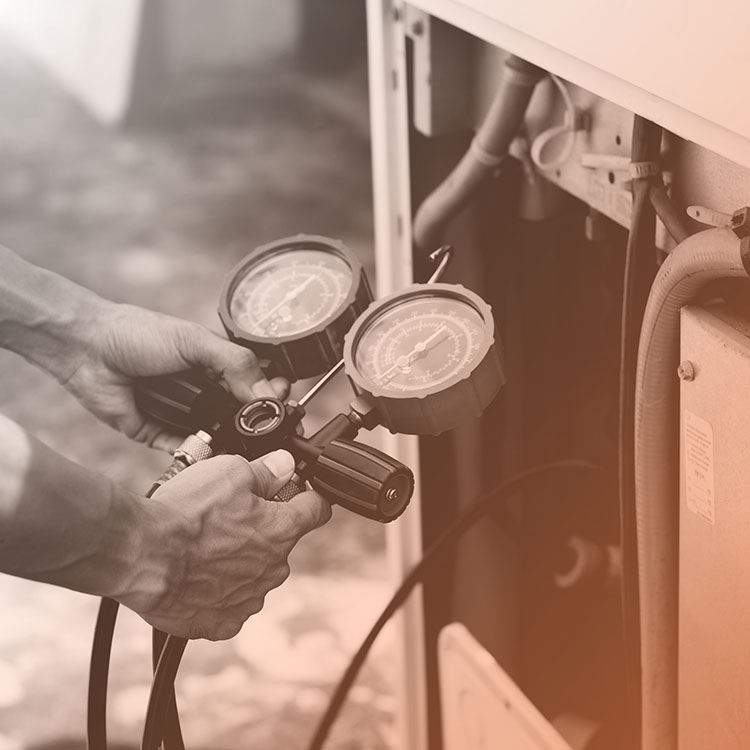
Nos offres
Simplifiez la gestion
de votre infrastructure
Notre plus grande fierté
Plus de 120 clients satisfaits:
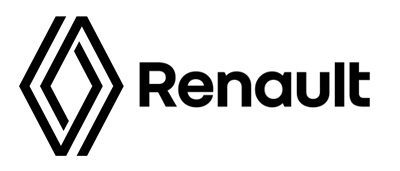
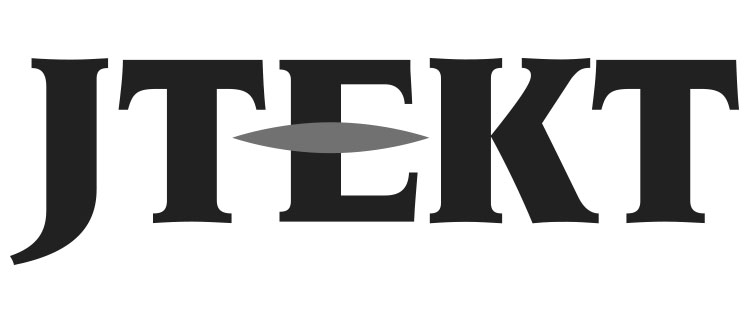
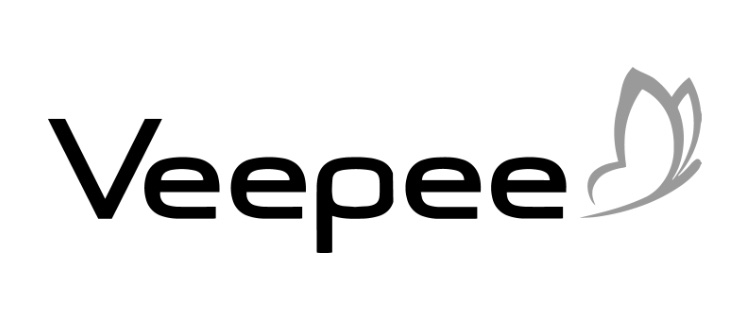
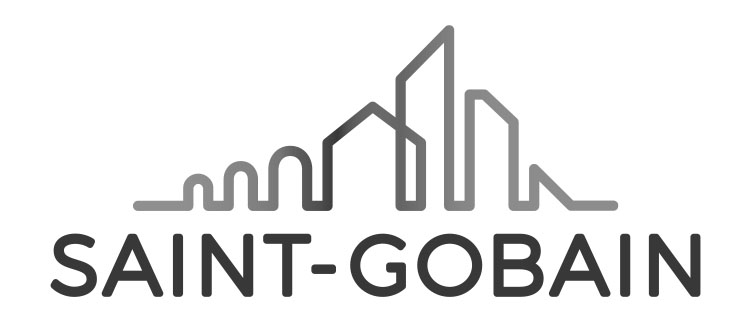
5
agences en France
8.3 M€
prévisionnel CA 2024
120
clients réguliers
24h
délai d’intervention
100